Design Of Balls In The Ball Mill
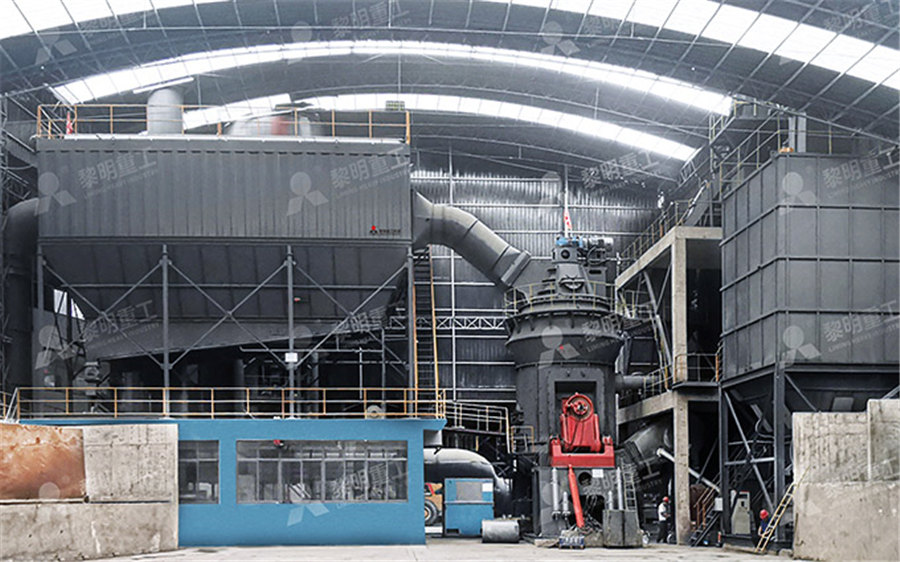
(PDF) Grinding in Ball Mills: Modeling and Process Control
2012年6月1日 The design of a ball mill can vary significantly depending on the size, the equipment used to load the starting ma terial (feeders), and the system for discharging the output product2021年3月12日 Ball mills and grinding tools Cement ball mills are typically twochamber mills (Figure 2), where the first chamber has larger media with lifting liners installed, providing the BALL MILLS Ball mill optimisation Holzinger ConsultingIn its simplest form, the ball mill consists of a rotating hollow cylinder, partially filled with balls, with its axis either horizontal or at a small angle to the horizontal The material to be ground may be Ball Mill an overview ScienceDirect TopicsThe design of a ball mill can vary significantly depending on the size, the equipment used to load the starting material (feeders), and the system for discharging the output product The size of a Grinding in Ball Mills: Modeling and Process Control
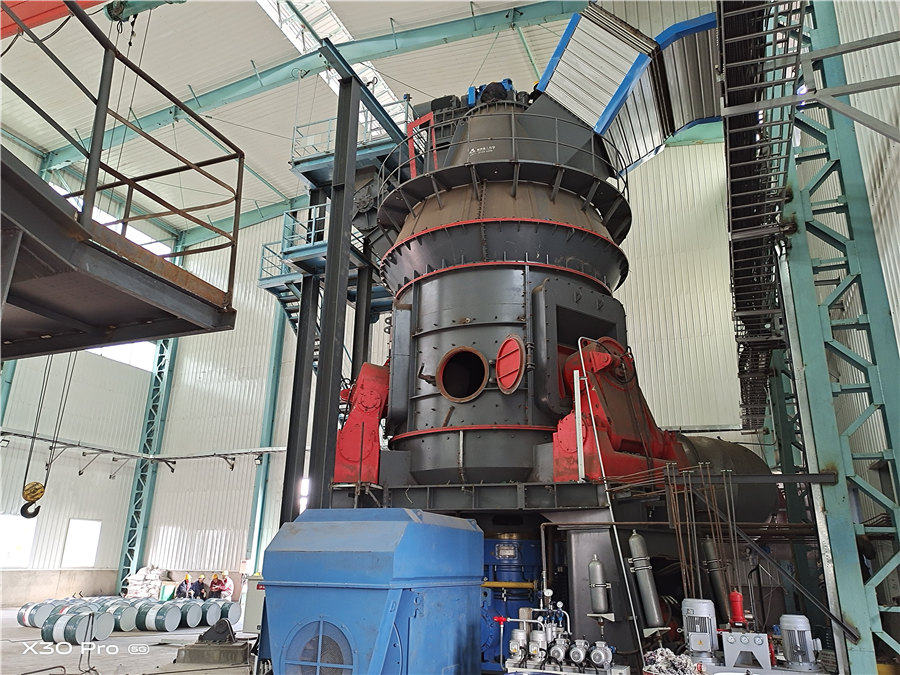
Design of horizontal ball mills for improving the rate of
2021年3月1日 The objectives of the present study were to: i) develop a model of horizontal ball mill by Solidworks and calculate collision energy by DEM simulation; ii) optimize the existing 2024年9月24日 This paper covers theoretical and experimental explorations for the sake of determining the optimal ball charge in millsTHE OPTIMAL BALL DIAMETER IN A MILL 911 2018年10月9日 Professor Saito and Senior Assistant Professor Kano at Tohoku University for the purpose of establishing a method for scaleup using rocking ball mill simulations In this Design Method of Ball Mill by Discrete Element Method2021年1月1日 According to the specifications and parameters of the ball mill, the general layout, grinding body, lining plate, partition device, support device, transmission part and feeding and Design of Threechamber Ball Mill IOPscience
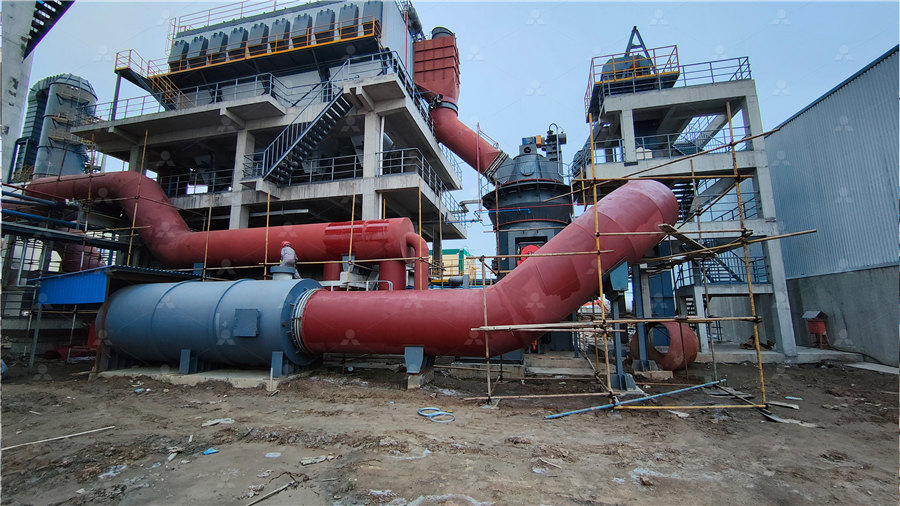
Design, fabrication and performance analysis of mini ball miller
2021年1月1日 The ball milling design significantly depends on the size of mill jar, required particle size distribution of powder and grinding media (balls) [13], [14], [15] The main purpose The design principle of ball mill steel balls is usually designed according to the requirements and characteristics of the ball mill to ensure stability and efficiency of the ball mill In a ball mill, the motion state of grinding balls is affected by Ball Mill Balls Manufacturing Of High Quality 2024年10月3日 The cylinder is the container that holds the ball mill grinding process together We size cylinders by their total volume when empty When selecting a cylinder, it’s important to pick a size that could potentially hold all of your grinding media, raw materials, and 25% of your total volume for processing space—what we consider the "working" area of the ball millUnderstanding the Parts of a Ball Mill Economy Ball MillBall mills are simple in design, consisting of horizontal slow rotating vessels half filled with grinding media of ¼” to 15” The particles to be milled are trapped between the grinding media or balls and are reduced in size by the actions of Ball Mill Application and Design Paul O Abbe
.jpg)
Ball Mills 911Metallurgist
2017年2月13日 Here this Ball Mill Design Calculator Where the finished product does not have to be uniform, (1″—1½”) balls and possibly tertiary ball mill with 20 mm (¾”) balls or cylpebs To obtain a close size distribution in the fine range the specific surface of the grinding media should be as high as possible Thus as small balls as 2023年4月23日 between the ball mill a nd rod mill showed that particles in a ba ll mill h ave a shorter residence time than in a rod mill [5 8] This is because balls offer less resistance to t he flow of (PDF) Grinding Media in Ball MillsA Review ResearchGate1997年12月1日 Undoubtedly the limited inroads that simulation has made in ball mill circuit design is due to the historic success of Bond's method [1] in crusherball mill and rod mill ball mill circuits [10] Its dependence is therefore on the rate at which the mill rotates, the volume of balls in the mill, and the slurry holdup Hence: VBN VI, , (7 Using modelling and simulation for the design of full scale ball mill 2021年3月12日 Ball mills and grinding tools Cement ball mills are typically twochamber mills (Figure 2), where the first chamber has larger media with lifting liners installed, providing the coarse grinding stage, whereas, in the second chamber, medium and fine grinding is carried out with smaller media and classifying linersBALL MILLS Ball mill optimisation Holzinger Consulting

Design of horizontal ball mills for improving the rate of
2021年3月1日 The purpose of this study is to optimize the existing collision model and design horizontal ball mill to examine the influence of the internal structure on the collision energy of mechanochemical reaction and should be increased as much as possible during the process of designing the horizontal ball mill The balls with at least 30 mm The characteristic tumbling motion of these mills has given them the name ‘tumbling mills’, which include the ball mill, tube mill and rod mill Ball mills are horizontal rotating cylindrical or conical steel chambers, approximately one third to half full of steel, alloy steel or iron balls, like that shown in Fig 410 A–C , or flint stonesBall Mill an overview ScienceDirect TopicsThe working principle of a ball mill is based on the impact and attrition between the balls and the grinding media As the mill rotates, the grinding media (usually steel or ceramic balls) are lifted to a certain height and then allowed to fall freely, causing the materials to be reduced in size by the impact and abrasive forces generated Ball Mill Grinding Machines: Working Principle, Types, Parts 2024年9月24日 ball that sits against the lifter and plate (Royston, 2001) At constant mill speed, ball trajectories should degrade (ie, balls fall more towards the bulk of the charge than the toe) with time as the lifters wear down Shell lifters with initially large face angles may start by directing ball impacts at the toeSemiautogenous grinding (SAG) mill liner design and
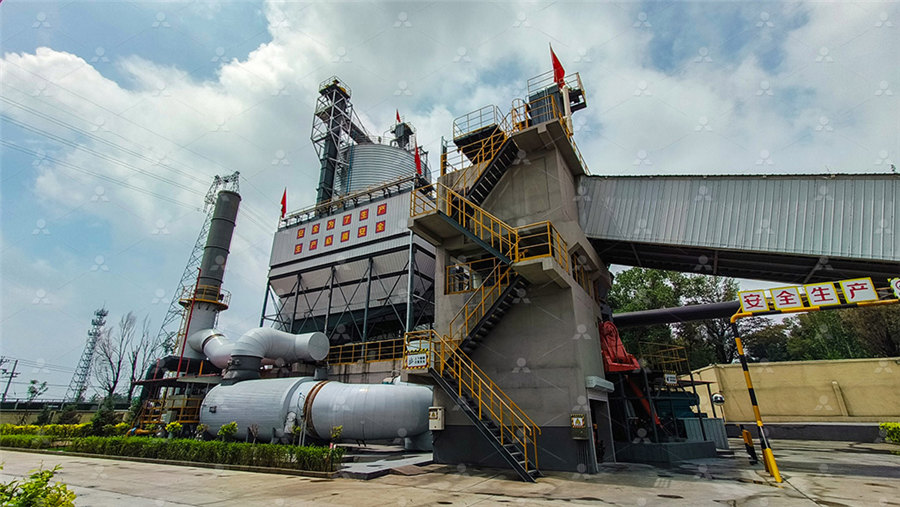
Analyzing the influence of lifter design and ball mill
lifter number, and mill rotational speed on mill performance In their work, the DEM simulations are compared with the experimental results Li et al [15] simulate the particle motion in a ball mill for five distinct lifter shapes at various rotational speeds Rectangular lifters and 2021年1月1日 Comchambered with the design of Φ 35 × 13m threechamber ball mill, the design process of ball mill is described in detail General arrangement of the mill Filling rate of grinding body in each (PDF) Design of Threechamber Ball Mill2016年4月25日 This project is to design and fabricate the mini ball mill that can grind the solid state of various type of materials into nanopowder The cylindrical jar is used as a mill that would rotate the (PDF) DESIGN AND FABRICATION OF MINI BALL MILL METHODOLOGY 2014年10月10日 Design and Analysis of Ball Mill For Paint Industries Mayur H Patel1 Mr Vishal A Pandya 2 1MEMachine Design pursuing2Asst Prof predicted on the assumption that the ball mill is half filled with balls, there is a cascade angle of 45o, and the mill base just covers the top layer Fig1: Optimum cascading of mill for power consumption Design and Analysis of Ball Mill For Paint Industries IJSRD
.jpg)
Ball Mill Rod Mill Design 911Metallurgist
2016年4月22日 Grinding (Rod) or (Ball) Mill TYPE D Has single weld, triple flanged, construction which means the shell is furnished in two sections, flanged and bolted in the center All flanges are double welded as well as steel head to shell, note design Tumbling Mill (Rod or Ball) Mill TYPE E Has quadruple flanged construction This also furnishes mill 2017年11月6日 Ball Design Factors Size and Mass Importance of size: Taggart (1927) stated “Size of balls should be proportional to the work to be done, ie the size of the particle that must be broken by impact, hence coarse feed and hard ores require larger balls than finer feeds and softer ores” The 9 to 10 m (30 to 33 ft) SAG mills now in wide use Grinding Ball Design 911Metallurgist2017年7月5日 The effects of major processing parameters of attritor mills on ball milling efficiency (ie, minimum energy consumption with maximum milling progress) are investigated using discrete element modeling (DEM)The major processing parameters investigated include the size of balls, ball volume fraction inside the canister, ball milling velocity, and design of the Modeling and Analysis of HighEnergy Ball Milling Through Attritors The size, shape, and design of the ball mill can vary depending on the nature of the material being processed, the desired particle size, and the processing capacity required Factors to Consider If you want a fine powder, you will need a smaller ball mill with smaller balls, whereas a larger ball mill with larger balls is required for How to Choose the Right Type of Ball Mill for Your Application
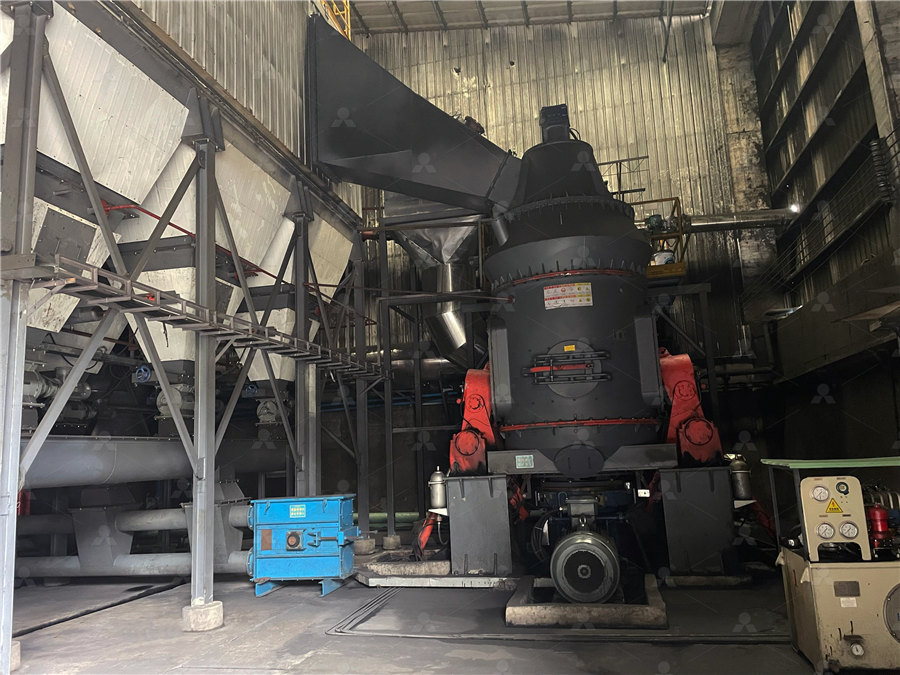
Ball Mills and Ball Charging Bulk Handling Technologies
This design uses heavy duty support rollers to drive the rotation of the mill shell directly Depending on the, the drive and support rollers can be polyurethane lined rollers or a series of rubber tyres Bulk Handling Techonolgies can design and supply roller mounted ball mills with capacities ranging from 500 kg/hr up to 25 TPH in a single mill2022年11月30日 Several types of ball mills exist They differ to an extent in their operating principle They also differ in their maximum capacity of the milling vessel, ranging from 0010 liters for planetary ball mills, mixer mills, or Ball Mill: Operating principles, components, 2023年10月27日 The ball mill is a rotating cylindrical vessel with grinding media inside, which is responsible for breaking the ore particles Grinding media play an important role in the comminution of mineral ores in these mills This work reviews the application of balls in mineral processing as a function of the materials used to manufacture them and the mass loss, as A Review of the Grinding Media in Ball Mills for Mineral 2024年7月12日 A ball mill and a tumbling mill are both types of grinding mills used to reduce material size We mainly use a ball mill for mixing and grinding processes In contrast, we generally use a tumbling mill for finer material What Is a Ball Mill and How Does It Work?
.jpg)
Ball Mill Liner Design 911Metallurgist
2016年1月5日 In rod mill work the design is such that they will easily pass through the large ball open end discharge trunnion Where cast liners are used, and especially in rod mill applications, we furnish rubber shell liner backing to help cushion the impact effect of the media within the mill and prevent pulp racing2021年3月1日 The purpose of this study is to optimize the existing collision model and design horizontal ball mill to examine the influence of the internal structure on the collision energy Studies have shown that not only the collision between balls, but also the collision between the balls and internal structure (balls and blades, balls and cylinder Design of horizontal ball mills for improving the rate of 2022年1月1日 The ball mill is used for the conversion of the raw stone material into the powder form by using steel balls inside The ball mill is a cylindrical form of container that is driven by a toothed circular gear by couple of gears present in the gear box The gear box is a setup intended for making the power transmission from the electric motor to Design and simulation of gear box for stone crushing ball millThere are three types of grinding media that are commonly used in ball mills: • steel and other metal balls; • metal cylindrical bodies called cylpebs; • ceramic balls with regular or high density Steel and other metal balls are the most frequently used grinding media with sizes of the balls ranging from 10 to 150 mm in diameter [30]Grinding in Ball Mills: Modeling and Process Control
.jpg)
Design, fabrication and performance analysis of mini ball miller
2021年1月1日 The ball milling design significantly depends on the size of mill jar, required particle size distribution of powder and grinding media (balls) [13], [14], [15] The main purpose of milling process is to obtain required particle size of the powder without any contamination, increasing the output of the milling circuit and overall reduction in 2020年5月19日 The ball mill liner replacement should in time when the lining plate is excessively worn Therefore, the selection and design of mill liners have always been of great concern to users Function Design of Ball Mill Liners As one of the professional ball mill liners manufacturers, we summarize the main functions of the threepoint ball mill linersBall Mill Liners Selection and Design Ball Mill Rubber Liner2024年8月13日 The cylinder is rotated by a motor, and the grinding media are placed inside the mill The design of a ball mill incorporates the following components: 1 Shell: The shell is the outer covering of the ball mill, providing structural integrity and protecting the internal components It is commonly made of steel or other durable materials 2 Exploring the functionality and design of ball mills2024年6月1日 From equation (7): K m, is the thermal Conductivity of the container’s material; A, is the area of the bottom of the container; e, is the thickness of the container; T si, is the temperature of DESIGN OF A BALL MILL TYPE ATTRITOR FOR THE
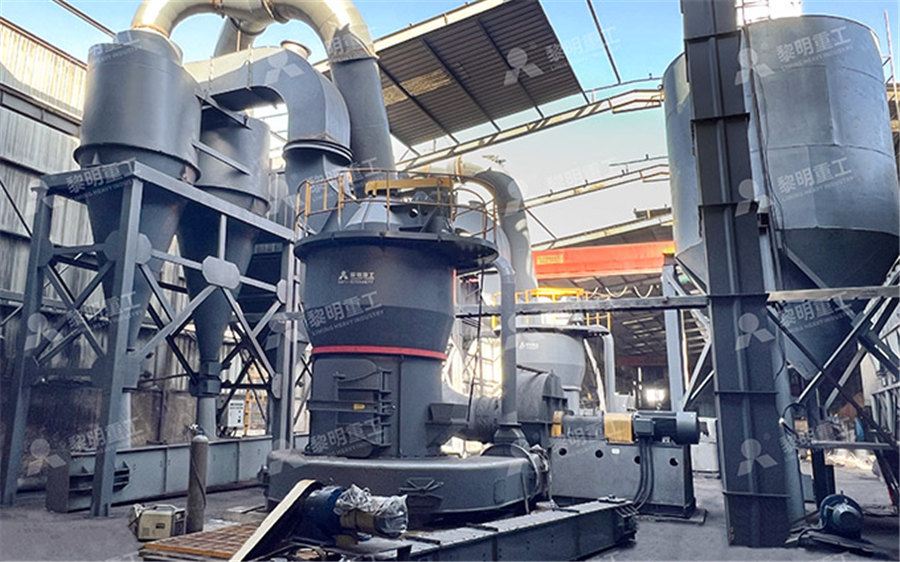
Ball Mill Success: A StepbyStep Guide to
2024年8月8日 Unlock the secrets to ball mill efficiency with our comprehensive guide on choosing the right grinding media Learn how material composition, size, shape, hardness, and cost impact your milling process and outcomes Steel 2024年4月28日 Critical Speed: Critical speed is the hypothetical speed at which the centrifugal force is equal to the gravitational force, and the grinding media starts sticking to the inner shell of the equipment instead of falling What is a Ball Mill Explained: InDepth Guide2016年4月25日 With a view to developing a sound basis for the design and scaleup of ball mills, a large amount of data available in the literature were analyzed for variation of the two key mill performance (PDF) Design and Fabrication of Mini Ball Mill (edited)2023年11月14日 The ball mill is a rotating cylindrical vessel with grinding media inside, which is responsible for breaking the ore particles This work reviews the application of balls in mineral processing as a function of the materials used to manufacture them and the mass loss, as influenced by three basic wear mechanisms: impact, abrasion, and A Review of the Grinding Media in Ball Mills for Mineral
.jpg)
Understanding production of fines in batch ball milling for mill
2018年9月1日 There are two main approaches to the scaleup design of ball mills: (expressed as fraction of the mill volume occupied by balls at rest, J); and particle load (expressed as fraction of the void volume of the static ball charge occupied by particles, U), the magnitude and nature of variation in the rate of production of fines are found to be 2024年10月23日 The basic parts of the ball mill are a shell, balls, and motor Fig2 A ball mill is also known as a pebble mill or tumbling mill It consists of a hollow cylindrical shell (drum) containing balls mounted on a metallic frame such that it can be rotated along its longitudinal axis It has a simple design, ease of examination, and change of Ball Mill Principle, Construction, Working, and More Soln 2024年7月12日 Conversely, a speed that is too fast can cause excessive ball movement, where the balls remain flush with the drum walls due to centrifugal force, reducing the grinding efficiency Ball mills are indispensable tools in the material processing industry They harness the power of motion to transform coarse materials into finely ground Walking Through the Ball Milling Process Economy Ball Mill2017年4月29日 In the previous discussion the fact was established that the work done by a ball when it strikes at the end of its parabolic path is proportional to its weight and velocity; then, since the velocity may be considered as constant for all the balls in the mill, the work done by a ball is proportional to its weight Since the amount of ore crushed varies as the work done upon it, it Grinding Media Wear Rate Calculation in Ball Mill
.jpg)
RoM BALL MILLS A COMPARISON WITH AG/SAG
2024年7月24日 RoM Ball mills, like SAG mills, utilise coarse rocks in the RoM feed as grinding media but with 25 – 40% steel balls added, which is advantageous when the coarse fraction in the RoM feed is